Do you know these surface treatment processes?
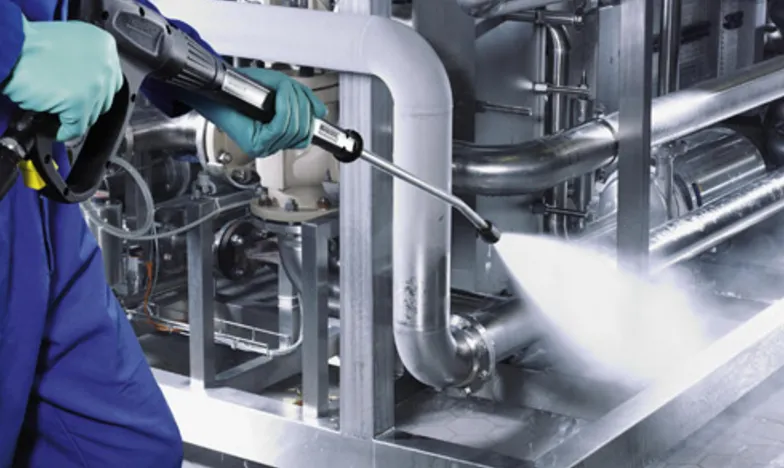
Surface treatment is a process that uses the marginal new technologies of modern physics, chemistry, metallurgy, heat treatment and other disciplines to change the condition and properties of the surface of parts to meet the predetermined performance requirements.
Common surface treatment methods
Surface modification technology
Through physical and chemical methods, the morphology, phase composition, microstructure, defect state and stress state of the material surface are changed. The chemical composition of the material surface remains unchanged.
01 Surface Quenching
Surface quenching refers to a heat treatment method that uses rapid heating to austenitize the surface layer and then rapid cooling (quenching) to harden the surface without changing the chemical composition and structure of steel.
02 Sandblasting
Sandblasting is a process that uses the sand or iron particles sprayed at high speed to impact the workpiece surface, so as to improve some mechanical properties of parts and change the surface state.
The process of sand blasting and shot blasting is similar, and the main difference is in the diameter of sand particles. This process is mainly used to improve the mechanical strength, wear resistance, fatigue resistance and corrosion resistance of parts. It can also be used for surface extinction, scale removal and residual stress elimination of castings, forgings and weldments.
03 Rolling
Rolling is a treatment process in which hard rollers or rollers are pressed on the rotating workpiece surface at room temperature and move along the bus direction to make the workpiece surface plastic deformation and hardening, so as to obtain an accurate, smooth and strengthened surface, or a specific pattern.
04 Wire Drawing
Under the action of external force, the metal is forced through the mold, the cross-sectional area of the metal is compressed, and the required cross-sectional area shape and size are obtained. The technical processing method is called metal wire drawing process. The tool that makes it change shape and size is called drawing die. Wiredrawing can be made into straight lines, random lines, corrugations, threads, etc. according to decorative needs.
05 Polishing
Polishing is a finishing method to modify the surface of parts. Generally, it can only get a smooth surface, and cannot improve or even maintain the original processing accuracy. With different pre-processing conditions, the Ra value after polishing can reach 1.6 ~ 0.008 mm. According to the different implementation principles, it can be divided into mechanical polishing and chemical polishing.
06 Laser Surface Strengthening
Laser surface strengthening is to use the focused laser beam to shoot at the surface of steel parts, heat the extremely thin material on the surface of the workpiece to the temperature above the phase transformation temperature or melting point in a very short time, and then cool it in a very short time to harden and strengthen the surface of the workpiece. Laser surface strengthening can be divided into laser phase transformation strengthening treatment, laser surface alloying treatment and laser cladding treatment.
Laser surface strengthening has small heat affected zone, small deformation and convenient operation. It is mainly used for locally strengthened parts, such as blanking die, crankshaft, cam, camshaft, spline shaft, precision instrument guide rail, high-speed steel cutter, gear and cylinder liner of internal combustion engine.