Selection of Solid Welding Wire
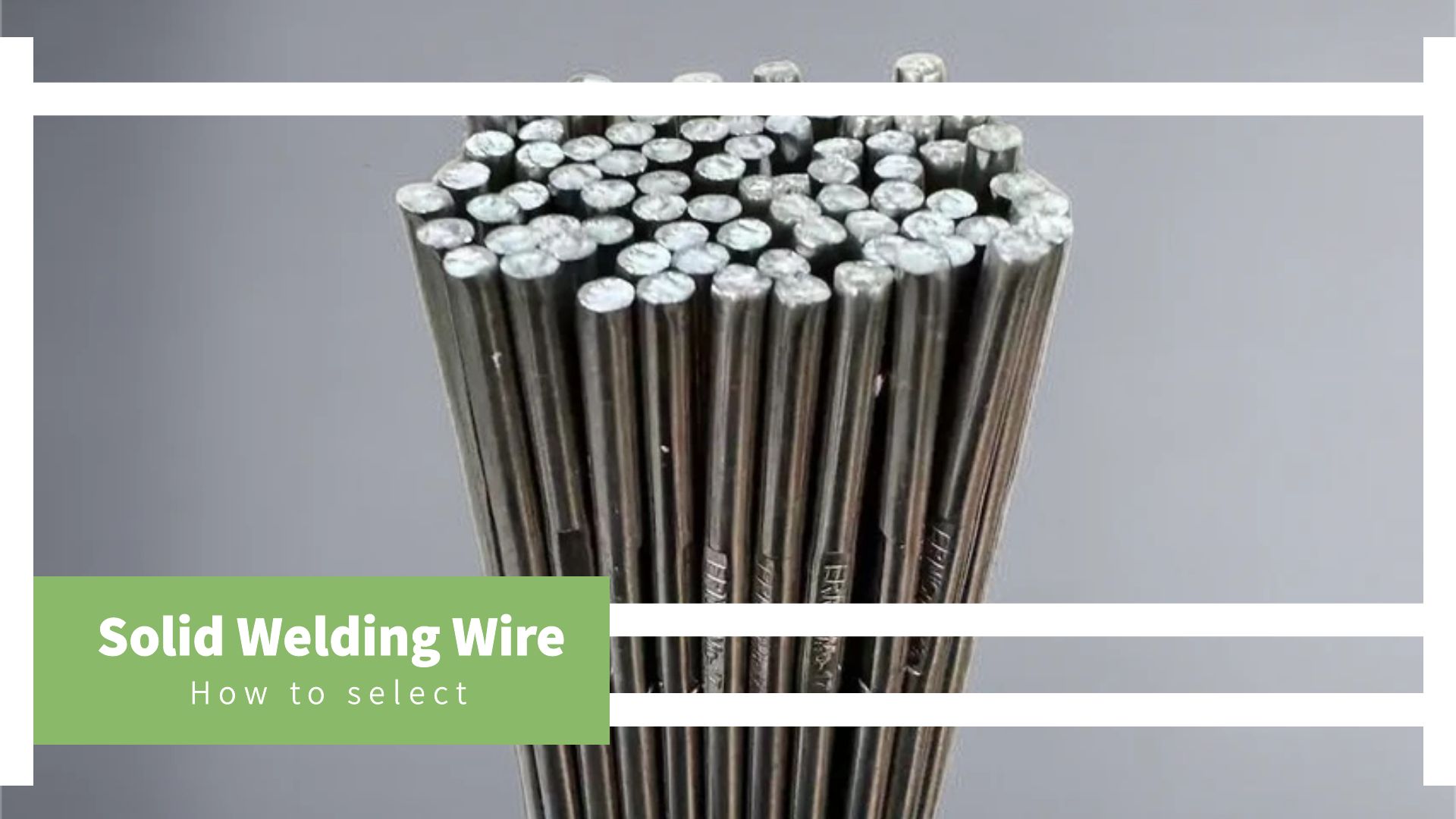
01丨Welding Wire for Submerged Arc Welding
In the process of submerged arc welding, the welding wire serves the dual purpose of filling metal and introducing alloying elements into the weld while participating in metallurgical reactions that protect and treat the weld metal.
- During submerged arc welding of low carbon steel and low alloy steel, the following three types of welding wires are commonly employed:
- A. Low manganese welding wire (e.g., H08A): Typically used in conjunction with high manganese flux for welding low carbon steel and low-strength low alloy steel.
- B. Medium manganese welding wire (e.g., H08MnA, H10MnS): Mainly utilized for welding low alloy steel and can also be used with low manganese flux for welding low carbon steel.
C. High manganese welding wire (e.g., H10Mn2, H08Mn2Si): Employed in welding low alloy steel.
This category of welding wire contains over 1% manganese and 0.3% to 0.8% molybdenum, such as H08MnMoA and H08Mn2MoA, suitable for welding high-strength low alloy steel. Depending on the composition and performance requirements of high-strength steel, elements such as Ni, Cr, V, and Re can be added to the welding wire to enhance weld metal properties. Welds with a tensile strength of 590MPa often use MN-MO series welding wires like H08MNMOA.
02丨Welding Wire for Gas Shielded Welding
Gas-shielded welding includes inert gas-shielded welding (TIG and MIG welding), active gas-shielded welding (MAG welding), and self-shielded welding. In TIG welding, pure Ar gas is typically used, while MIG welding generally employs Ar+2%O2 or Ar+5%CO2 gas mixtures. MAG welding mainly relies on CO2 gas. To improve the performance of CO2 welding, CO2+Ar or CO2+Ar+O2 gas mixtures can be used, along with flux-cored wires.
In TIG welding, sometimes no additional filler wire is needed, and the base material is melted and directly connected. However, filler wire may be used in some cases. Since TIG welding uses pure Ar gas, which is non-oxidizing, the composition of the filler wire remains largely unchanged after melting, making it identical to the weld's composition. In some instances, the base material's composition is used as the filler wire's composition to match the weld with the base material. TIG welding uses lower welding energy, resulting in welds with good strength, plasticity, and toughness that easily meet performance requirements.
3) CO2 Welding Wire:
03丨Welding Wire for Submerged Arc Welding
04丨Welding Wire for Non-Ferrous Metals and Cast Iron
Welding wire codes with the first two letters "HS" indicate wires for non-ferrous metals and cast iron. The first digit in the code represents the wire's chemical composition type, while the second and third digits represent different wire grades of the same type.
Currently, hardfacing with hard alloy welding wires mainly falls into two categories: high chromium alloy cast iron (e.g., Solmaryte) and cobalt-based alloys (e.g., Stellite). High chromium alloy cast iron exhibits excellent oxidation resistance and corrosion resistance, high hardness, and good wear resistance. Cobalt-based alloys maintain high hardness and good corrosion resistance even at high temperatures (650°C). Some have lower carbon and tungsten for improved toughness, while those with high carbon and tungsten have high hardness but reduced impact resistance. The hard alloy hard-facing welding wire can be used for hardfacing using oxy-acetylene or gas welding methods. While oxy-acetylene hard-facing has lower production efficiency, it offers simple equipment, shallow penetration during hard-facing, minimal base material melting, and high hard-facing quality, making it widely used.
Copper and copper alloy welding wires are commonly used for welding copper and copper alloys, with brass welding wire also widely used for brazing carbon steel, cast iron, and hard alloy cutting tools. Welding copper and copper alloys can employ various welding methods, with the correct choice of filler metal being essential to obtain high-quality welds. When using oxy-acetylene gas welding, it is advisable to use it in conjunction with gas welding flux.
Aluminum and aluminum alloy welding wires are used for aluminum alloy argon arc welding and oxy-acetylene gas welding as filler materials. The choice of welding wire is mainly based on the type of base material, joint cracking resistance, mechanical properties, and corrosion resistance requirements. In most cases, welding aluminum and aluminum alloys should use wires with the same or similar grades as the base material to ensure good corrosion resistance. However, when welding heat-treated aluminum alloys with a high risk of hot cracking, the choice of welding wire primarily focuses on crack resistance, and the composition of the welding wire may differ significantly from the base material.