Types, Explanations, and Key Applications of Spring Wires
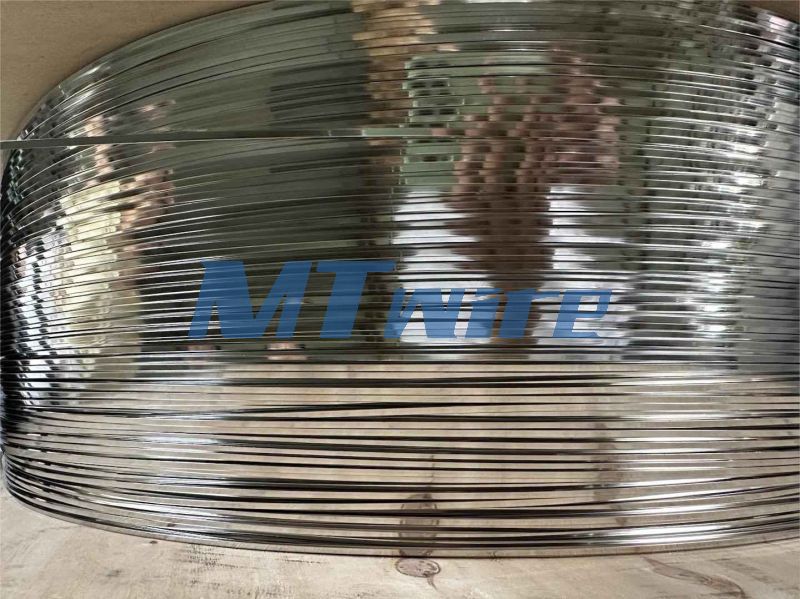
Springs, vital components in industrial manufacturing, serve crucial roles across diverse sectors like machinery, electronics, and aerospace. Yet, distinct contexts demand specific spring wires for optimal performance and reliability. This article delves into the breadth of spring wires, spotlighting nickel-based alloys, carbon steels, and stainless steels, uncovering their traits, areas of application, and pivotal role in spring production. Let's explore the distinctiveness of each wire and how they offer tailored spring solutions to varying industrial demands.
Nickel Alloys
These alloys excel in corrosion resistance and mechanical properties under extreme heat and conditions. They find application in crafting springs for high-temperature and corrosive settings, such as those found in gas turbine engine components.
Known for exceptional corrosion resistance, these alloys suit environments with corrosive agents, including chemical industries and marine domains. In spring manufacturing, they are used to create components functioning amidst corrosive gases or liquids.
Ideal for high-temperature corrosive settings, these alloys combine heat and corrosion resistance, making them prevalent in chemical and refining equipment.
These alloys are fitting for environments with high temperatures and corrosive media, serving applications in petroleum chemical and oil refining.
Hard nickel-based alloys excel in wear resistance and high-temperature performance, ideal for springs in high-speed machinery.
Carbon Steel
Piano wire, cold-drawn for excellent surface finish, boasts high magnetic and tensile strength, extending spring life.
These wires are suitable for ordinary low-pressure spring applications, gaining necessary properties through cold drawing.
Ideal for crafting regular springs, these wires offer high magnetic properties, with performance obtained through quenching and tempering.
Stainless steel
These stainless steel grades excel in corrosion and high-temperature resistance, apt for chemical, pharmaceutical, and food processing industries.
With lower nickel content, these stainless steel suit scenarios require relatively lower corrosion resistance.
These stainless steel alloys excel in corrosion resistance, ideal for applications like automotive exhaust systems.