Welding Wire Introduction
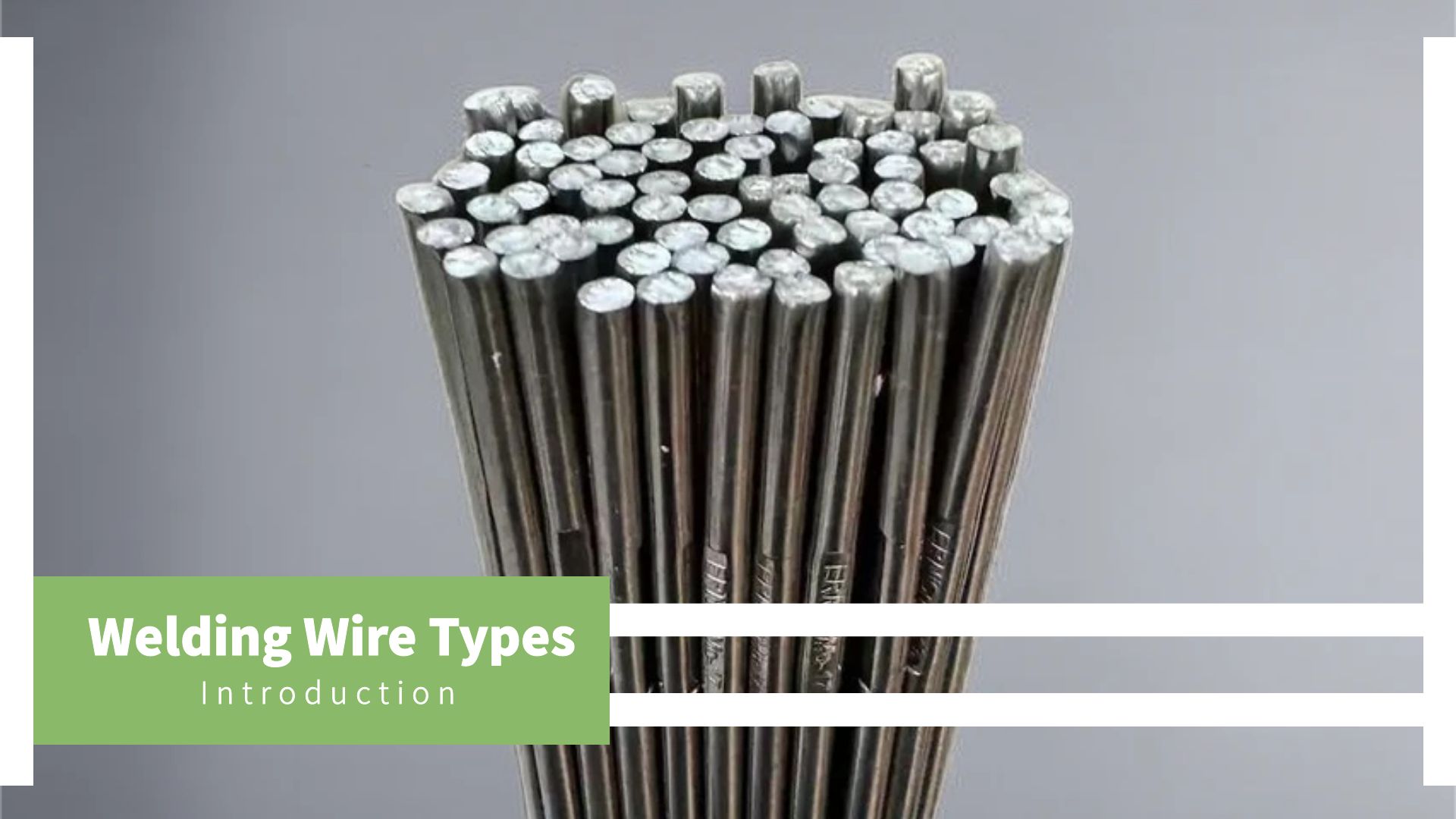
Welding wire is a very important material in metal welding. Stainless steel and nickel alloy wires, for example, have a wide range of applications in metal welding, especially in MIG, TIG, and submerged arc welding, and are the most widely used welding materials in the industry. Stainless steel solid wires and nickel alloy solid wires are preferred by users for their stable and excellent welding results.
Of course, in addition to the above two types of wire, we will also see aluminum wire, copper and aluminum wire, copper wire and other types of wire, as well as according to the function of the classification of wear-resistant wire, submerged arc wire, laser wire and so on. Choosing the right wire is the key to welding work because different wires have different properties and characteristics, suitable for different welding environments and needs.
The following is a detailed description of the different types of welding wire.
Stainless Steel Welding Wire:
This wire is suitable for both shielding gas welding (TIG, MIG welding), also suitable for submerged arc welding, and stainless steel MIG welding can achieve both high-efficiency welding, but also easy welding automation, and is widely used in the field of surfacing and thin plate joining. According to different needs, you can choose stainless steel solid wire. Stainless steel welding wire has good corrosion resistance and heat resistance, so it is widely used in many high-end manufacturing fields.
Nickel Alloy Welding Wire:
A welding material with excellent performance in high-pressure, high-temperature, and corrosive environments, its corrosion resistance, high-temperature stability, and excellent mechanical properties make it widely used in electric power, petroleum, chemical, aviation, food, and nuclear industries. Especially in its corrosion resistance, which can effectively deal with acid and alkaline environments; it's unique high-temperature stability so that it can maintain the original physical and chemical properties at high temperatures; and excellent mechanical properties in a variety of mechanical applications to provide a guarantee. Its welding performance is excellent, welded joints have good toughness and crack resistance, but it requires professional welding technology and equipment for welding so as not to cause structural and performance problems of welded joints.
Aluminium-Aluminium Welding Wire:
Aluminum-aluminum welding wire, also known as aluminum-aluminum flux-cored wire, the special feature of this wire is that it can weld aluminum materials together without the need to use visible welding machine welding. It is different from the ordinary aluminum welding wire to be welded with the apparent lonely welding machine, also different from the aluminum-silicon welding wire needs to cooperate with the brazing flux in order to weld, but only through the flame or induction can be brazed directly welding. Aluminum welding wire welded from the workpiece tensile shear strength, electrical conductivity, and corrosion resistance are better and more stable quality, so it has a wide range of applications in the field of shipbuilding, automobile manufacturing, and other aluminum product manufacturing.
Copper-Aluminium Welding Wire:
Copper and aluminum welding wire is a kind of flame-hard nail welding material, through the flame-brazing process, copper and aluminum are two different materials welded together, because the center of the welding wire including Shu's so-called flux-cored wire, eliminating the need to weld before the need to dip the welding powder step, improve productivity. This flux-cored wire is a new material, in the power and electronics industry and has a very important application.
Silver Welding Wire:
This type of wire is mainly used in the production and maintenance of food industry components, containers, pipes, electrical plugs, surgical equipment, ophthalmic equipment, and precision parts used in mechanical and electromechanical industries. Silver welding wire is widely used in electronics and precision engineering due to its good electrical conductivity and oxidation resistance.
In general, the choice of welding wire must be based on the actual welding needs and environment to be considered, choosing the wrong wire may lead to unsatisfactory welding results and may even affect the quality and performance of the product. There is no best welding wire, only the most suitable welding wire. We hope this article will help you to better understand the welding wire for your welding job.