Mig Welding Wire
Nickel Alloy ER600 Welding Wire for Chemical industry
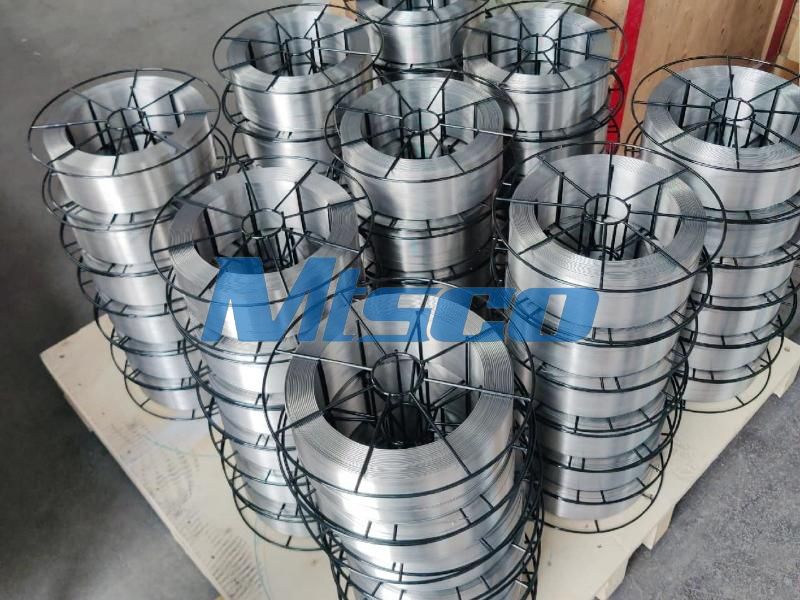
Nickel Alloy Wire is a class of high-performance wire materials consisting of nickel and other alloying elements. It is recognised for its excellent corrosion resistance, outstanding mechanical properties and high temperature stability. The wire material has a wide range of applications and meets the needs of a variety of critical areas. The main classifications are nickel alloy welding wire, nickel alloy spring wire, nickel alloy weaving wire, nickel alloy electrical resistance wire and so on.
Nickel Alloy ER600 Welding Wire for Chemical industry
Nickel Alloy ER600 Welding Wire is a high-performance nickel alloy welding wire composed of the alloying elements nickel and chromium. It has excellent corrosion resistance and thermal stability and is particularly suitable for applications in high-temperature and corrosive environments. The wire maintains mechanical properties over a wide temperature range and has good weldability. It is widely used in the chemical, petroleum, aerospace, and nuclear industries.
Advantageous features:
High-temperature stability: maintains mechanical properties in high-temperature environments, suitable for long-time use.
Excellent corrosion resistance: able to resist a wide range of corrosive media, including seawater and various acids.
Good processing performance: can be easily processed through conventional welding methods to meet diverse industrial needs.
Wide range of wire diameters: Maxtor offers a range of wire diameters from 0.15mm to 16mm, adapting to different application scenarios.
Chemical Composition:
Ni | Cr | Fe | Mn | C | Cu | Si | S | P | Co | Nb/Cb | Ti | Ta | Al | Mo | B | Pb | Bi | Se | |
Alloy 600 | >=72 | 14-17 | 6-10 | 1 | 0.1 | 0.5 | 0.5 | 0.015 | 0.04 | 1 | 1 | 0.5 | 0.05 | 0.35 | - | ||||
Alloy 601 | 58-63 | 21-25 | bal | 1 | 0.1 | 1 | 0.5 | 0.015 | - | - | - | - | - | 1-1.7 | - | ||||
Alloy 625 | >=58 | 20-23 | 5 | 0.5 | 0.1 | 0.5 | 0.5 | 0.015 | 0.015 | 1 | 3.15-4.15 | 0.4 | 0.05 | 0.4 | 8-10 | ||||
Alloy X750 | >=70 | 14-17 | 5.0-9.0 | 1 | 0.08 | 0.5 | 0.5 | 0.01 | - | 1 | 0.7-1.2 | 2.25-2.75 | 0.05 | 0.4-1.0 | - | ||||
Alloy 718 | 50-55 | 17-21 | bal | 0.35 | 0.08 | 0.3 | 0.35 | 0.015 | 0.015 | 1 | 4.75-5.5 | 0.65-1.15 | 0.05 | 0.2-0.8 | 2.8-3.3 | 0.006 | 0.0005 | 0.00003 | 0.003 |
Application areas:
Energy industry: for welding of nuclear reactors, heat exchangers and pipelines for oil and gas transportation.
Chemical industry: for welding of chemical reactors, distillation towers and piping systems, especially those components exposed to corrosive environments.
Aerospace: for the manufacture and repair of engine components for spacecraft and aircraft and other critical structures in high temperature environments.
Offshore: for the maintenance and repair of facilities and equipment in seawater environments, such as offshore platforms and ships.
Company Profile:
Quality Control
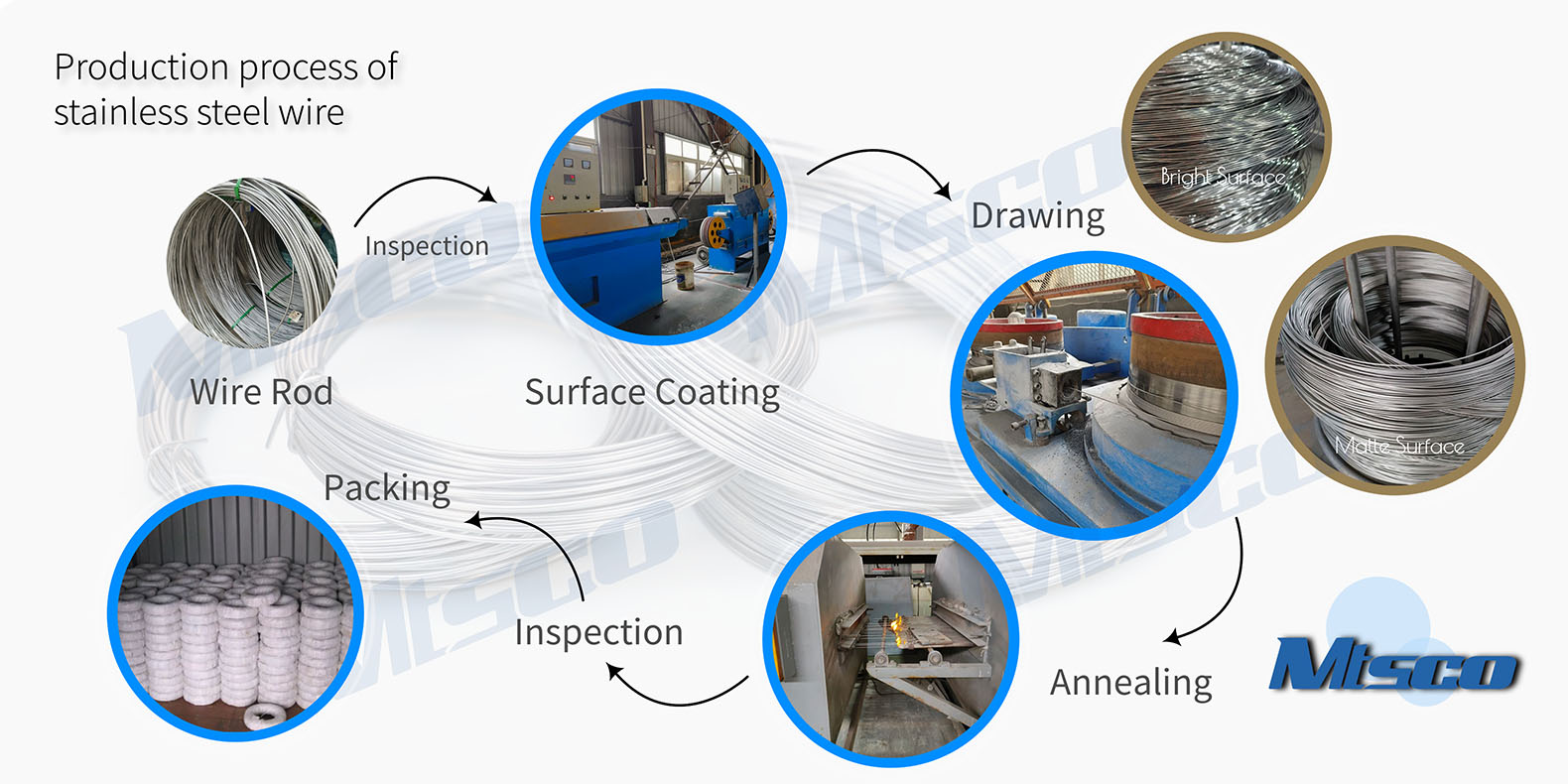
Why Choose MTSCO?

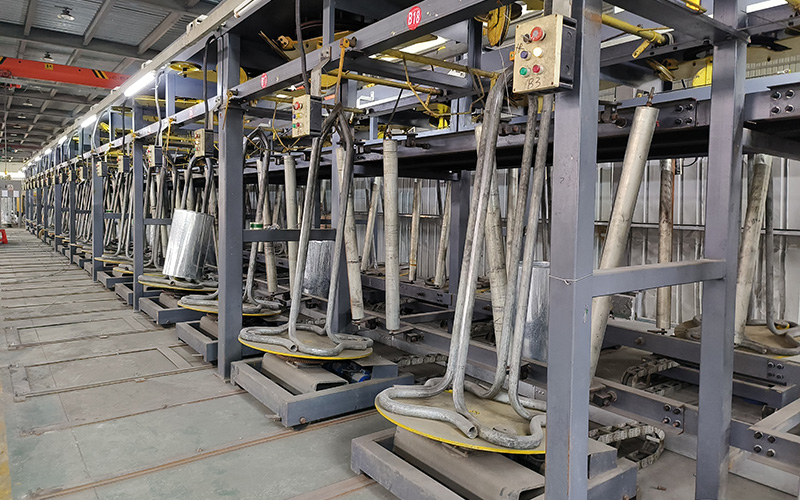
Integration of industry and trade
Provide you with cost-effective products and professional services.
One stop procurement of stainless steel wire products
Leave the complexity to Mtsco and the simplicity to you.
After the test of time for 17 years
Whether the products, services, capital and strength, Mtsco is your optimum partner.
Send Inquiry
*Required fields are marked.